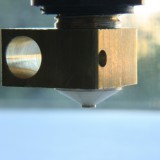
Jak widać społeczność RepRapowa w Polsce rośnie w siłę z dnia na dzień, na blogach pojawia się coraz więcej wpisów, a ilość aukcji wyskakująca na allegro po wpisaniu ‘RepRap’ już od dawna przekracza dwie strony
Od dłuższego czasu funkcjonują też dwa ciekawe miejsca do dyskusji : http://www.reprapforum.pl/ oraz http://www.mojreprap.pl/board/ (to drugie dostępne tylko po zalogowaniu). Wydaje mi się w takim razie, że pisanie o budowie/rozbudowie RepRapa mija się już z celem (informacje na ten temat są wszędzie), więc postanowiłem się podzielić kilkoma dość ważnymi spostrzeżeniami dotyczącymi tak zwanej ‘praktyki drukowania’.
O co chodzi ? Otóż głównym tematem będzie dziś ekstruder (znowu!;-). O ile o elektronice można powiedzieć ‘mózg maszyny’, to ekstruder będzie jej sercem – bo kiedy nie działa sprawnie, nawet najlepiej ustawiona elektronika/firmware nie pomoże. Aby działał dobrze, nie wystarczą tutaj dobre chęci i szybkie rozwiązania ‘ad hoc’, bo prowizorki zawodzą prawie zawsze. Widzę także (między innymi na Allegro), że pojawiają się rozwiązania wyglądające na solidne, ale niestety nie sprawdzone ‘w bojach’, a tym samym nie zawsze niezawodne. Aby zweryfikować, co (moim zdaniem) w ekstruderze jest najważniejsze, wykonałem w ciągu dwóch lat sporo testów. Na podstawie tych doświadczeń (kilka zniszczonych ekstruderów, dysze rozpadające się na części, palące się kable i wycieki plastiku) wypunktowałem najsensowniejsze założenia, które powinny być spełnione:
- strefa topienia plastiku powinna być krótka , nie długa. W starych dyszach tego typu strefa topienia jest średniej długości, co może być pożądane przy wydrukach na dużych prędkościach – można ją stosować z powodzeniem, ale zazwyczaj wymaga dłuższych retrakcji (zasysów) plastiku przy przemieszczaniu dyszy. Przy dłuższych strefach topienia zaczynają się problemy, takie jak wypływ plastiku do góry ekstrudera – to skutkuje wyciekami lub jego zastyganiem, co może zablokować dyszę.
Najprostszym sposobem na skrócenie strefy topienia jest zaprojektowanie dyszy tak, żeby miała w środku teflonową rurkę prowadzącą plastik. Filament będzie się wtedy lepiej ślizgał po ściankach, i roztopi się dopiero na samym końcu, kiedy dotknie gorącej końcówki dyszy przy wylocie.
- teflon jako materiał konstrukcyjny nie sprawdza się. W ekstruderach inspirowanych tym wymyślonym przez Adriana Bowyera (twórcę RepRapa) działa on z powodzeniem dla PLA (niższe temperatury), ale przy ABSie i podgrzaniu do 240-250 stopni staje się elastyczny. Jeśli w tym momencie działa na niego jakaś siła/naprężenie, odkształci się. To tyczy się także sytuacji, gdzie jest on przytrzymywany przez blok PEEK i dociskany do góry – jeśli nie będzie dociskany odpowiednio mocno, bądź pojawią się jakieś luzy pomiędzy dyszą a gwintem na teflonie, istnieje duże ryzyko, że plastik wypłynie na zewnątrz i zastygnie (duży problem, jeśli blob plastiku pochłonie kable i termistor).
W praktyce sytuacje takie nie zdarzają się często (np tylko wtedy gdy dysza zablokuje się jakimś śmieciem), ale jak to się już stanie, to ciśnienie w środku wzrasta na tyle, że plastik szuka ujścia gdzie tylko może – między innymi pomiędzy teflonem a mosiężną dyszą. Pomaga okręcenie gwintu taśmą do uszczelniania rur (też teflonową).
Generalnie, wniosek jest taki :
- najlepszym materiałem do budowy bariery termalnej w dyszy jest PEEK. Fakt, jest nieziemsko drogi (ponad 1000zł za kilogram), ale na szczęście bariera termalna za wiele nie waży. PEEK (polieteroeteroketon) w porównaniu do teflonu nie odkształca się pod wpływem wysokich temperatur (do 300 stopni), więc może również pełnić funkcje strukturalne. Jednym z najlepszych designów dyszy z PEEK jakie widziałem jest (moim zdaniem oczywiście, bo to subiektywny artykuł J-head.
(ja sam używam z dużym powodzeniem dyszy zaprojektowanej przez 7h7, o dość podobnej konstrukcji).
Istnieją też dysze z barierą termalna zrobioną z aluminium, ale zazwyczaj zwiększa to jej gabaryty i długość, co nie jest najlepsze, bo zmniejsza rozpiętość osi Z.
- plastik po opuszczeniu dyszy musi mieć możliwość się schłodzić. Projekty bloków grzejnych, które wiszą bardzo nisko nad wydrukiem i mają dużą powierzchnię nie sprawdzają się przy drukowaniu małych obiektów. Blok grzejny oddaje ciepło w dół, nie pozwalając plastikowi zastygnąć, co skutkuje jego deformacją i podwijaniem się na rogach. Najlepsze są tutaj małe bloczki grzejne zawieszone trochę wyżej i pozwalające na swobodny przepływ powietrza pod spodem. Bardzo pomaga też odpowiedni kąt ścięcia dyszy (ok 40-45 stopni), i dodatkowy ‘dziubek’ na jej końcu – przez niego plastik układa się lepiej, szczególnie podczas drukowania tzw. ‘mostków’ (bridges). Poniższe zdjęcie ilustruje te założenia dość dobrze:
Można też próbować jakoś zaizolować spód bloku grzejnego, albo dodać wentylator – ale tak, żeby chłodził tylko plastik, nie dyszę. Bardzo fajne rozwiązanie wymyślił Wulfnor na swoim blogu (oraz opublikował pliki na thingiverse – sprytny pomysł na chłodzenie).
————————-
Tyle zatem a propos dyszy. Ale to jeszcze nie koniec… wiem, że do pełni szczęścia i długiego, bezawaryjnego drukowania potrzebna jest jeszcze cała reszta ekstrudera, tzn silnik+zębatki, no i oczywiście szeroko dyskutowany ‘hobbed bolt’, czyli ‘radełkowana’ śruba z dociskowym łożyskiem i sprężyną.
Najczęstsze problemy z powyższymi elementami to :
- za duża lub za mała moc silnika. Można ją regulować potencjometrem na driverze (tak tak, on po to tam jest:-) . Jeśli jest za mała, silnik nie będzie się wyrabiał przy retrakcjach i dużych prędkościach druku. Jeśli jest za duża, to śruba będzie wrzynać się w plastik gdy napotka duży opór (np przy szybkich fragmentach wydruku) i może wyżłobić w nim rowek, który zablokuje dalsze przesuwanie filamentu.
Co zrobić ? Najlepiej wyregulować potencjometr tak, żeby znaleźć punkt ‘graniczny’ i dać silnikowi tylko tyle mocy ile potrzebuje. Jeśli zgubi raz na jakiś czas kilka kroków, ale pracuje i wypluwa plastik normalnie, jest to dobry znak – chodzi głównie o to, że nie będzie na siłę pchał plastiku, jeśli nie ma na to warunków. Wyobraźmy sobie, że na chwilę spadnie temperatura głowicy, albo do środka dostanie się jakiś paproch i zablokuje wypływ. Jeśli silnik ma pełną moc, wryje się wtedy ząbkami śruby w plastik i wydruk przepada. Jeśli zamiast tego zgubi trochę kroków i przeczeka trudny moment – za chwilę będzie drukował dalej, a nasz wydruk dotrwa do końca.
Mimo, że sytuacje te nie zdarzają się często, warto się w powyższy sposób zabezpieczyć – przydaje się to bardzo, szczególnie podczas długich wielogodzinnych wydruków bez naszego dozoru.
- niewłaściwe przygotowanie śruby tłoczącej plastik (hobbed bolt). Śruba najlepiej tłoczy głębokimi zębami (radełkowaniem?) wykonanymi gwintownikiem M4 albo M5 (M4 jest lepszy, bo powierzchnia styku z obwodem plastiku jest większa). Łuk gwintowania M5 jest większy, więc powierzchnia styku mniejsza. Z kolei przy wykorzystaniu gwintu M3 – zęby są zbyt płytkie i plastik będzie się ślizgał.
- za słaby docisk sprężyny na ekstruderze. To akurat trudno opisać obiektywnie, ale można by powiedzieć, że da się to wyczuć kręcąc kołem ekstrudera ręką (przy wyłączonych silnikach – Gkod M84, ale przy nagrzanej głowicy). Docisk sprężyny powinien być bardzo silny, ale na tyle, żeby kołem można jeszcze było kręcić ręcznie. U mnie śruba dociskająca sprężynę jest tak ustawiona, że ze sporym wysiłkiem jestem jeszcze w stanie odgiąć blok dociskowy (Idler) na 1-2mm do tyłu, ale nie więcej. Jeśli docisk jest za słaby, to śruba będzie się ślizgać po filamencie.
- zapychanie się śruby zerwanym plastikiem (wiórki). Zdarza się to wtedy , gdy notorycznie drukujemy za szybko lub na za niskiej temperaturze. Może też się wydarzyć, gdy głowica dotyka stołu, a my próbujemy ekstrudować plastik (zatkany wylot). Rezultat wygląda mniej więcej jak na poniższych fotkach :
Przy takim stadium zapchania śruby trzeba ją poprosty wyciągnąć i wyczyścić. Z praktyki jednak wiem, że jeśli usuniemy przyczynę (np zwiększymy temperaturę lub zmniejszymy prędkość druku – na Marlinie można to zrobić ‘na gorąco’) – śruba potrafi stopniowo oczyścić się sama. Można też próbować czyścić ją podczas druku – ale potrzeba trochę gimnastyki (da się!
A na koniec najgorszy z możliwych problemów, czyli :
- zapchanie wylotu głowicy. Ojjj… to chyba jeden z najbardziej niefajnych przypadków , gdzie potrzebna będzie czasem kompletna reanimacja ekstrudera. Zdarza się to bardzo bardzo rzadko – ale jak już się zdarzy, to trudno to naprawić. Symptomy :
- wiórki na śrubie
- bardzo powolny wypływ plastiku
- kiedy próbujemy wepchnąć plastik ręką do komory topiącej, czujemy duży opór (możemy to sprawdzić kręcąc ręcznie kołem ekstrudera – po uprzednim wyłączeniu silników – Motors Off w Pronterface , lub odpinając docisk i wpychając filament dłonią).
Wydarza się to wtedy, gdy w środku dyszy jest jakiś obiekt, który jest większy niż jej wylot. Może to być śmieć/paproch który przykleił się wcześniej do szpuli filamentu, albo (według niektórych bloggerów) przypalony fragment plastiku, który się ‘zwęglił’.
Jak sobie z tym poradzić ? Są dwie metody. Pierwsza to kompletne rozłożenie głowicy na części i oczyszczenie jej ręcznie (niektórzy polecają przepalenie jej palnikiem, jak tutaj ). Druga – przepchanie otworu igłą. Można to zrobić przy nagrzanej głowicy używając kombinerek jak na fotografii poniżej, czasem się udaje Trzeba próbować do skutku.
A generalnie najlepszą metodą zapobiegania takim sytuacjom jest ‘filament cleaner’, czyli poprostu kawałek szmatki ściągającej kurz i śmieci z plastiku, zanim wejdzie on do ekstrudera.
W tym odcinku ‘pamiętnika’ to już tyle, następnym razem postaram się napisać już więcej o samym drukowaniu i kilku ciekawych trickach (będzie też trochę o nowych slicerach – m.in. Slic3r i Cura)
Po walkach ze śrubą extrudera moim faworytem jest poprzeczne nacięcie linii na śrubie z pełnym gwintem. Robią się wtedy jakby kolce. Dzięki temu, że na śrubie nacięty jest gwint poprzeczne podcięcia nie mają tendencji do zapychania się. Ogólnie z tego rozwiązania jestem najbardziej zadowolony. Fakt, że trochę wtedy należy przerobić otwór w obudowie extrudera bo filament idzie trochę po łuku, ale “co Ciebie nie zabije to Cię wzmocni:
Racja, to jest też bardzo dobre rozwiązanie – nawet próbowałem taką śrubę zrobić, ale gwintownik na nic tu się nie zda, trzeba to nacinać dremelem. Powstały nawet fajne urządzenia do robienia takich śrub, indeksujące rowki : http://www.thingiverse.com/thing:10110
a co do łuku, to polecam nowy ekstruder Grega Frosta, z guidlerem ( http://www.thingiverse.com/thing:17030 ) – fajnie prowadzi filament, i ma inny otwór.
No właśnie ja dremlem i frezem rzeźbiłem
amatorka podzielnica z Thingiverse – fajna sprawa – muszę coś podobnego do mojej frezarki zmotać
there are many caveats to consider with Scotiabank. There is a huge housing bubble swirling in Canada. Some analysts fear that this bubble may create an issue for Canadian banks. If Canada’s housing bubble bursts Scotiabank holds 16% of modern mortgage book. CEO Rick Waugh said that Canada’s housing marketplace is suffering a soft landing. “Our amount you are behind rates with our customers are showing slightly elevated, But not good deal (spikes) Are well within check,