Wśród wielu zastosowań druku 3d na pierwszy plan wysuwają się te, gdzie trzeba stworzyć pojedyncze obiekty lub bardzo krótkie serie dostosowane do konkretnej potrzby/sytuacji. Pięknym przykładem jest drukowany szkielet dla niepełnosprawnej dziewczynki:
The video cannot be shown at the moment. Please try again later.
(dzięki za linka Tomek!)
Dla mnie, poza fajnymi emocjami, to wideo pokazuje problematyczność zastosowania druku 3d w codziennym życiu. Na filmie widać jak wyoko opłacany specjalista (a zapewne kilku) spędza tygodnie na zaprojektowaniu jednego urządzenia. I choć sam druk zapewne nie kosztuje dużo, to wysiłek zaprojektowania użytecznego obiektu jest bardzo kosztowny.
To jedno podejście do tematu – tworzenie rzeczy na indywidualne zamówienia. Jak wie każdy, kto tego próbował, jest to na tyle trudne, że przeciętny Kowalski nie będzie chciał się nauczyć projektrować 3d, żeby coś sobie wydrukować.
Z drugiej strony mamy Thingiverse czy Shapeways, gdzie są gotowe produkty. Wybieramy z listy, wybieramy materiał i drukujemy, względnie płacimy i drukują dla nas. Pod względem projektowania bułka z masłem, ale jesteśmy jednocześnie ograniczeni do tego co stworzyli inni.
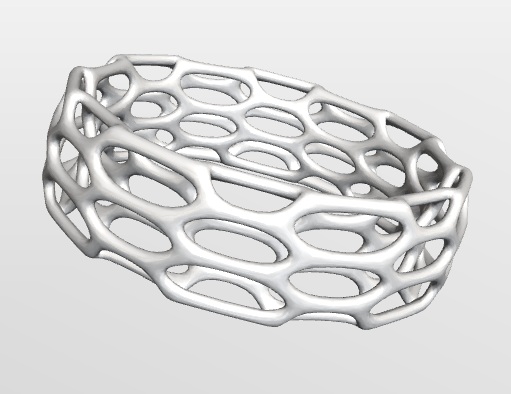
Myślę jednak, że jednym z kluczy do upowszechnienia druku 3d i użycia jego siły, jest to co znajduje się pomiędzy opisanymi wyżej skrajnościami: szybkie dostosowywanie istniejących projektów do konkretnego klienta/potrzeby. Choćby poprzez automatyzację projektowania lub stworzenie do tego na tyle prostych narzędzi, żeby ów Kowalski potrafił to zrobić sam. Przykłady już są. Można przez sieć dostosowywać sobie świeczniki, lalki, bransolety czy inne rzeczy.
Idac krok dalej i trochę bujając w obłokach i można pomyśleć o podobnych rozwiązaniach dla zastawy stołowej, mebli, lamp czy innych powszechnie kupowanych i uważanych za “dizajnerskie” obiektów. Można też wyobrazić sobie automatyczne tworznie obiektów po przeskanowaniu w 3d osoby/wnętrza.
Sądzę, że dopiero takie wyeliminowanie trudności projektowania przyczyni się do przyniesienia druku 3d pod strzechy.
Ostatnie komentarze